1.Precautions for welding operation
When welding, the operation should be carried out strictly according to the steps, otherwise, the quality of welding will be affected.
(1) The surface of the pipe fittings to be welded should be clean or flared. The flared mouth should be smooth, round, free of burrs and cracks, and uniform in thickness. Polish the copper pipe joints to be welded with sandpaper, and finally wipe them with a dry cloth. Otherwise it will affect the solder flow and soldering quality.
(2) Insert the copper pipes to be welded overlapping each other (pay attention to the size), and align the center of the circle.
(3) When welding, the welded parts must be preheated. Heat the welding part of the copper pipe with a flame, and when the copper pipe is heated to purple-red, use a silver electrode to weld it. After the flame is removed, the solder is leaned against the solder joint, so that the solder melts and flows into the soldered copper parts. The temperature after heating can reflect the temperature through the color.
(4) It is best to use a strong flame for fast welding, and shorten the welding time as much as possible to prevent excessive oxides from being generated in the pipeline. Oxides will cause dirt and blockage along the flow surface of the refrigerant, and even cause serious damage to the compressor.
(5) When soldering, when the solder is not completely solidified, never shake or vibrate the copper pipe, otherwise the soldered part will have cracks and cause leakage.
(6) For the refrigeration system filled with R12, it is not allowed to weld without draining the R12 refrigerant, and it is not possible to perform welding repairs when the refrigeration system is still leaking, in order to prevent the R12 refrigerant from being toxic due to open flames. Phosgene is poisonous to the human body.
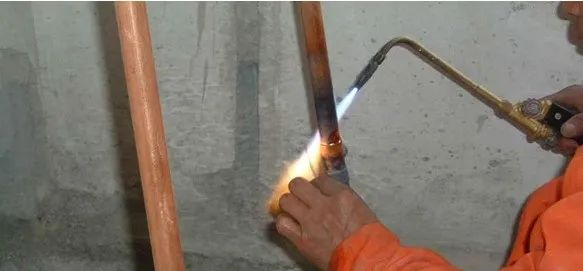
2. Welding method for different parts
(1) Welding of phase diameter pipe fittings
When welding copper pipes with the same diameter in the refrigeration system, use casing welding. That is, the welded pipe is expanded into a cup or bell mouth, and then another pipe is inserted. If the insertion is too short, it will not only affect the strength and tightness, but also the flux will easily flow into the pipe, causing contamination or blockage; if the gap between the inner and outer pipes is too small, the flux cannot flow into the containment surface and can only be welded to the outside of the interface. The strength is very poor, and it will crack and leak when subjected to vibration or bending force; if the matching gap is too large, the flux will easily flow into the pipe, causing pollution or blockage. At the same time, leakage will be caused by insufficient flux filling in the weld, not only the quality Not good, but also a waste of materials. Therefore, it is extremely important to choose the insertion length and the gap between the two pipes reasonably.
(2) Welding of capillary tube and copper tube
When repairing the filter drier of the refrigeration system, the capillary tube (throttle capillary tube) should be welded. When the capillary is welded to the filter drier or other pipes, due to the large difference in the two pipe diameters, the heat capacity of the capillary is very small, and the phenomenon of overheating is extremely prone to increase the metallographic grain of the capillary, which becomes brittle and easy to break. In order to prevent the capillary from overheating, the gas welding flame should avoid the capillary and make it reach the welding temperature at the same time as the thick tube. A metal clip can also be used to clamp a thick copper sheet on the capillary tube to increase the heat dissipation area appropriately to avoid overheating.
(3) Welding of capillary tube and filter drier
The insertion depth of the capillary should be controlled within the first 5-15mm, the insertion end of the capillary and the filter dryer should be 5mm from the end of the filter screen, and the matching gap should be 0.06~0.15mm. The end of the capillary is best made into a horseshoe-shaped 45° angle to prevent foreign particles from staying on the end surface and causing blockage.
When the two pipe diameters are very different, the filter drier can also be crushed with a pipe clamp or a vise to flatten the outer pipe, but the inner capillary cannot be pressed (dead). That is, insert the capillary tube into the copper tube first, and squeeze it with a pipe clamp at a distance of 10 mm from the end of the thick tube.
(4) Welding of refrigerant pipe and compressor conduit
The depth of the refrigerant pipe inserted into the pipe must be 10mm. If it is less than 10mm, the refrigerant pipe will easily move outwards during heating, causing the flux to block the nozzle.
3. Inspection of welding quality
In order to ensure absolutely no leakage at the welded part, necessary inspections should be carried out after welding.
(1) Check whether the sealing performance of the weld is good. After adding refrigerant or nitrogen to stabilize for a certain period of time, it can be tested with soapy water or other methods.
(2) When the refrigerating and air-conditioning operation is in operation, no cracks (seams) in the welding place due to vibration should be allowed.
(3)The pipeline should not be blocked due to debris entering during welding, nor should it enter moisture due to improper operation.
(4) When the refrigeration and air-conditioning work, the surface of the welding part should be clean and free of oil stains.
Post time: Oct-23-2021